GRINDCLEAN RESOURCES HUB
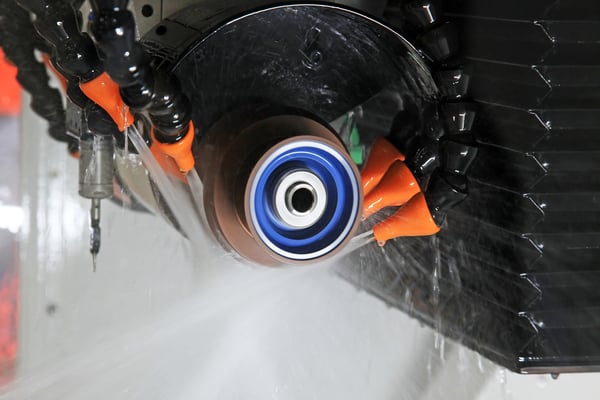
COOLANT RESOURCES & TECHNICAL SUPPORT
At Eagle Superabrasives, we understand that choosing and maintaining the right industrial coolant is essential for grinding performance, tool longevity, and machining efficiency. Our Resources Hub is designed to provide valuable insights, expert guidance, and troubleshooting tips for manufacturers, machinists, and engineers working with cutting fluids and metalworking coolants.
STAY INFORMED WITH OUR BLOG
Our blog delivers industry news, expert tips, and in-depth comparisons to help you make informed decisions about your grinding coolants and cutting fluids.
INDUSTRIES SERVED
GrindClean Coolants are used across a wide range of high-precision machining industries, ensuring optimal performance and longevity.
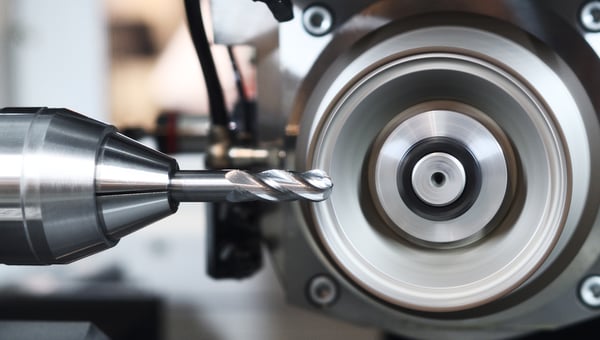
OUR COOLANTS ARE
TRUSTED IN:
-
Aerospace – High-performance coolants for tight-tolerance components
-
Automotive – Fluids designed for high-speed grinding and finishing
-
Tool & Die – Lubrication and cooling solutions for hard metals and alloys
-
Medical Manufacturing – Ultra-pure coolants for surgical and dental tool grinding
-
CNC Machining – Advanced cutting fluids for automated grinding systems
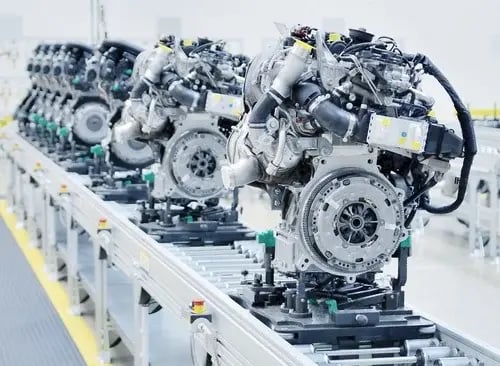
SUCCESS STORIES & CASE STUDIES
- How a leading aerospace manufacturer reduced grinding defects by 40%
- Automotive supplier increased tool life by 30% with our synthetic coolant
- Medical tool grinding: achieving precision with our water-soluble coolant
TECHNICAL SUPPORT & TROUBLESHOOTING
Proper coolant maintenance is crucial for achieving consistent grinding results and extending the life of your tooling and grinding wheels.
Frequently Asked Questions (FAQs)
We’ve compiled answers to the most common coolant-related questions to help you maximize efficiency and troubleshoot issues.
What’s the best coolant for my grinding operation?
This is going to depend on the following variables
What material(s) are you grinding? (e.g., carbide, HSS, stainless steel, titanium, aluminum)
What type of grinding are you doing? (e.g., surface grinding, centerless grinding, cylindrical grinding, creep feed, tool & cutter grinding, burr grinding)
What type of machine are you using? (e.g., manual grinder, CNC, high-speed grinder)
Are you using a diamond or CBN wheel, or a conventional abrasive?
Do you prefer oil-based or water-based coolant?
Any specific needs like:
-
Maximizing lubricity (for better surface finish)
-
Best cooling (to avoid burning or cracking)
-
Minimal foaming
-
Low maintenance / long sump life
-
Health & safety/environmental friendliness (e.g., low misting, non-hazardous)
We can help you with application specific coolant selection.
How often should I change my coolant?
Good question — and the honest answer is: it depends on how well you maintain it.
Here’s a clear breakdown:
You should change your coolant when:
-
pH drops or rises outside the recommended range (typically pH 8–9.5 for grinding coolants)
-
Concentration drops too low (from dilution) or climbs too high (from evaporation)
-
Coolant smells bad (bacterial or fungal growth — "rotten egg" or "musty" smell)
-
Heavy tramp oil buildup that skimming/vacuuming can't keep under control
-
Foaming that won't stop even after adding defoamer
-
Rust or corrosion appears on parts or machines
-
Poor grinding performance (burning, poor finish, clogging wheels)
Why is my coolant foaming, and how do I fix it?
Step 1: Identify why it’s foaming
Foaming isn't random — it usually has one or more causes:
-
Coolant is too thin (too much water, concentration too low)
-
Wrong mixing method (adding water to coolant instead of coolant to water)
-
High-pressure pumps / air entrainment (lots of agitation)
-
Contamination (tramp oils, cleaners, incompatible additives)
-
Coolant is old and breaking down
-
Water hardness is too low (soft water increases foaming)
Step 2: Quick Fixes to Try First
Action | Why It Helps |
---|---|
Check concentration with a refractometer | If too low, raise to the correct % (usually 3–7% depending on the coolant) |
Mix properly | Always add coolant into water, not the other way around |
Reduce pump pressure or bypass air leaks | Less agitation = less foam |
Use a compatible defoamer | Temporary help — many coolant suppliers sell defoamers |
Skim tramp oil | Oil films trap air and cause persistent foam |
Top off with properly mixed coolant | Not just water — topping off only with water dilutes and destabilizes coolant |
How do I properly dispose of used coolant?
Good question — and it’s important because improper coolant disposal can cause big legal, environmental, and cost problems.
Here’s a clear, correct way to handle used coolant disposal:
1. First: Understand the Law
-
In the U.S., used metalworking fluid (coolant) is often considered industrial waste.
-
It can become hazardous waste if:
-
It contains heavy metals (like lead, chromium, or cadmium) above limits.
-
It is contaminated with solvents or oils.
-
-
If hazardous, you must follow strict EPA rules (and probably local/state rules too).
-
If non-hazardous, you still cannot just dump it down a drain without permission.
2. Options to Dispose of Coolant Properly
Method | Best For | Notes |
---|---|---|
Hire a licensed waste hauler | Most common | They collect and properly treat/dispose of used coolant. |
On-site coolant treatment | Larger operations | Systems separate oil, metals, and clean water. Treated water may be sewered (if permitted), sludge hauled away. |
Evaporation | Small volumes | Evaporate water off (using an approved unit), then dispose of concentrated sludge properly. |
Recycle / Reclaim | Certain clean coolants | Specialized companies filter and purify the coolant for reuse. |
3. Before Disposal: Important Steps
-
Test the coolant (optional but recommended)
Especially for heavy metals or solvent contamination. -
Separate tramp oils and solids
Skim off floating oils; settle out sludge if possible. -
Recordkeeping
Maintain disposal receipts and manifests for at least 3 years. Required by EPA/state inspectors. -
Label drums or totes properly
Example: "Waste Coolant — Non-Hazardous" or "Waste Coolant — Hazardous" (after testing).
What are the key differences between oil-based and water-based coolants?
The coolant you can use depends on many variables including but not limited to the machine, the application, the material being ground, filtration etc.
You may also have specific needs when grinding that only certain coolant can provide.
Here is a general summary.
If You Need... | Best Choice |
---|---|
Maximum lubricity for tough materials or carbide grinding | Oil-Based |
Maximum cooling for high-speed grinding | Water-Based |
Lower maintenance and longer sump life | Oil-Based |
Lower cost | Water-Based |
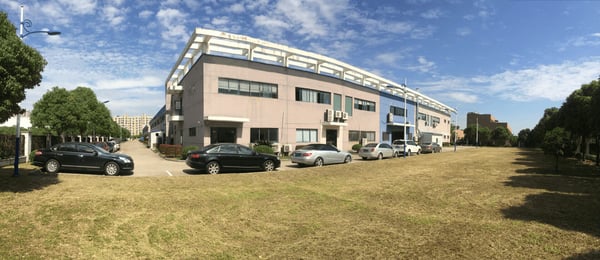
NEED HELP? CONTACT OUR COOLANT EXPERTS!
Our team of coolant specialists are here to assist you with product selection, troubleshooting, and bulk order inquiries.
Call Us Today or
Request a Quote