Explore the critical role of hardbanding in enhancing the durability drilling equipment in the harsh environments of downhole drilling.
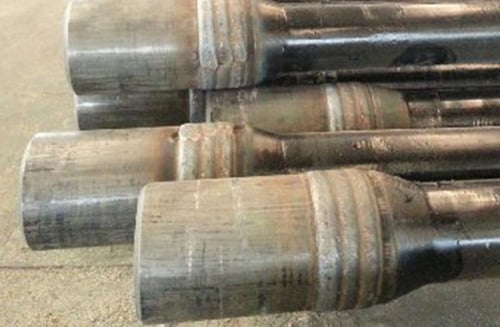
The Basics of Hardbanding: Definition and Importance
Hardbanding is a process where a protective layer of material is applied to the surfaces of drilling tools and equipment, particularly in the mining and downhole drilling industries. This layer is designed to enhance the durability of the equipment, reducing wear and tear caused by the harsh and abrasive conditions encountered during drilling operations. By minimizing the wear on drill pipes and other components, hardbanding helps extend the lifespan of the equipment, leading to cost savings and increased efficiency.
The importance of hardbanding cannot be overstated, as it plays a critical role in maintaining the integrity and functionality of drilling tools. Without this protective layer, equipment would be more susceptible to damage, leading to more frequent replacements and repairs. Hardbanding thus ensures that drilling operations can continue smoothly, minimizing downtime and enhancing overall productivity.
Materials and Techniques Used in Hardbanding
Various materials are used in the hardbanding process, each selected for their specific properties and suitability to the conditions of downhole drilling. Common materials include tungsten carbide, nickel-based alloys, and other hard metals that provide excellent resistance to wear and abrasion. The choice of material depends on factors such as the type of rock formations being drilled and the specific requirements of the drilling operation.
The techniques used in applying hardbanding involve welding or thermal spraying the protective material onto the surfaces of the drilling equipment. These methods ensure a strong bond between the hardbanding material and the underlying metal, providing a durable and long-lasting protective layer. The application process must be precise and controlled to achieve optimal results, with specialized equipment and skilled technicians playing a crucial role in ensuring the quality of the hardbanding.
The Role of Hardbanding in Downhole Drilling Operations
In downhole drilling operations, the equipment is subjected to extreme conditions, including high pressures, temperatures, and abrasive materials. Hardbanding provides a critical line of defense against these harsh conditions, protecting the drill pipes and other components from excessive wear. This protection is especially important in directional drilling, where the equipment must navigate complex and challenging pathways through rock formations.
By reducing the wear on drilling equipment, hardbanding helps maintain the performance and reliability of downhole tools. This, in turn, leads to more efficient drilling operations, with fewer interruptions and lower maintenance costs. The enhanced durability provided by hardbanding also contributes to the safety of drilling operations, as it reduces the risk of equipment failure and associated hazards.
Innovations in Hardbanding: Diamond Wheels and Beyond
One of the significant innovations in the field of hardbanding is the use of diamond wheels for grinding and finishing the hardbanded surfaces. Diamond wheels are known for their exceptional hardness and ability to grind even the toughest materials with precision. In the context of hardbanding, they are used to smooth and shape the protective layer, ensuring that it meets the required specifications and provides optimal performance.
The use of diamond wheels represents a significant advancement in the hardbanding process, offering improved efficiency and accuracy. This innovation has led to better-quality hardbanding applications, with smoother surfaces and enhanced durability. As technology continues to evolve, further advancements in materials and techniques are expected, paving the way for even more effective and reliable hardbanding solutions in the mining and downhole drilling industries.
Subscribe to email updates
Subscribe to our blog to get the latest updates from the experts on Grinding Wheels! You can easily unsubscribe at any time