Carbide burrs, also known as rotary files, are essential tools in metalworking and other industries requiring precise material removal and finishing. These versatile tools are used for deburring, shaping, chamfering, and sculpting hard materials. This guide will explore the various shapes of carbide burrs, their specific applications, and how to choose the right burr for your task.
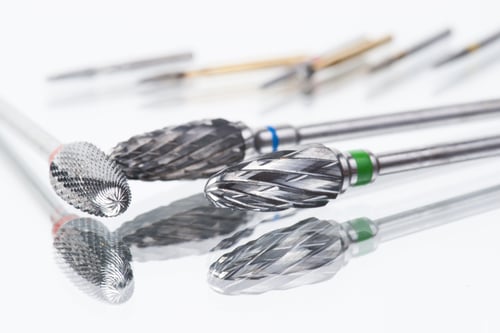
Understanding Carbide Burrs
Carbide burrs are cutting tools made from tungsten carbide, a material known for its hardness and durability. These burrs come in a variety of shapes, sizes, and spiral flutes each designed for specific applications. They are typically used on a shank in die grinders, rotary tools, and air tools for high-speed cutting, grinding, and material removal.
Common Carbide Burr Shapes and Their Applications
-
Cylinder Shape: Ideal for removing excess material from flat surfaces. It can be used for end cutting and produces a smooth finish.
-
Ball Shape: Perfect for creating concave cuts and hollowing out areas. It is commonly used for material removal in rounded profiles and intricate sculpting.
-
Oval Shape: Useful for rounded edges and contours. It offers a smooth finish on curved surfaces.
-
Tree Shape: There are two types of tree shapes - pointed and round. Pointed tree shapes are great for deburring and cutting in narrow places, while round tree shapes are excellent for rounding edges and shaping.
-
Cone Shape: cone burrs ar used for chamfering and beveling edges. It is effective for enlarging holes and deburring inside cuts.
-
Inverted Cone Shape: Ideal for making V-cuts and rear side chamfering. It can also be used for creating grooves and slots.
-
Flame Shape: Excellent for detailed work and fine cutting. It allows for precise control in tight spaces and detailed sculpting.
-
Ball Nose: Combines the features of ball and end-cut burrs, perfect for finishing and contour work on a workpiece.
-
Double Cut: Double cut carbide burrs feature two sets of cutting flutes arranged in different directions. This design allows for more cutting edges, which provides a smoother finish compared to single cut burrs. The flutes on double cut burrs intersect, creating smaller chips and reducing the chance of clogging.
-
Rotary burr: A rotary burr, also known as a rotary file, is a precision cutting tool used in a die grinder, rotary tool, or air tool for shaping, deburring, and finishing various materials
Selecting the Right Carbide Burr
When selecting a carbide burr, consider the material you are working with and the desired finish. Carbide burrs are effective on various materials, including:
-
Ferrous Metals: Stainless steel, cast iron, high-speed steel (hss), and other hard metals.
-
Non-ferrous metals: Aluminum, brass, and copper.
-
Plastics and Composites: Suitable for shaping and finishing without melting the material.
-
Ceramics: Ideal for precise cuts and smooth finishes on brittle materials.
-
Fiberglass: Effective for cutting and shaping without splintering.
Types of Carbide Burr Cuts
-
Single Cut: Features a single set of flutes running in one direction. It is designed for rapid stock removal, leaving a rougher finish. Best for use on steel, cast iron, and other ferrous metals.
-
Double Cut: Have two sets of flutes cut in different directions, providing a smoother finish and greater control. It is suitable for use on hard and soft metals, as well as plastics and wood.
-
Diamond Cut: Provides an even smoother finish and is designed for detailed work on harder materials.
Applications of Carbide Burrs
Tungsten carbide burrs are versatile tools used in various industries, including:
-
Aerospace: For precision deburring and shaping of components.
-
Automotive: For porting and polishing engine components.
-
Metalworking: For cutting, shaping, and finishing metal parts.
-
Jewelry Making: For intricate detailing and shaping of precious metals.
Tips for Using Carbide Burrs
-
Proper Speed: Ensure the die grinder or rotary tool operates at the correct speed for the burr size and material. High-speed applications typically work best with carbide burrs.
-
Coolant Use: When working with hard metals or materials prone to heat damage, using a coolant can extend the burr's life, enhance the cutting edges, and improve the finish.
-
Controlled Pressure: Apply consistent and moderate pressure to avoid damaging the burr or the workpiece. Excessive force can cause chipping or breakage.
-
Regular Cleaning: Clean the burrs regularly to remove material buildup, which can affect performance and finish.

Carbide burrs are indispensable tools for any professional or hobbyist involved in
metalworking, woodworking, or any task requiring precise
material removal and finishing. By understanding the different shapes and their applications, you can select the right
carbide burr for your needs and achieve
high-quality results on a variety of materials. Whether you're working with
stainless steel,
plastics,
ceramics, or
fiberglass,
carbide burrs provide the durability and efficiency needed for intricate and demanding tasks.